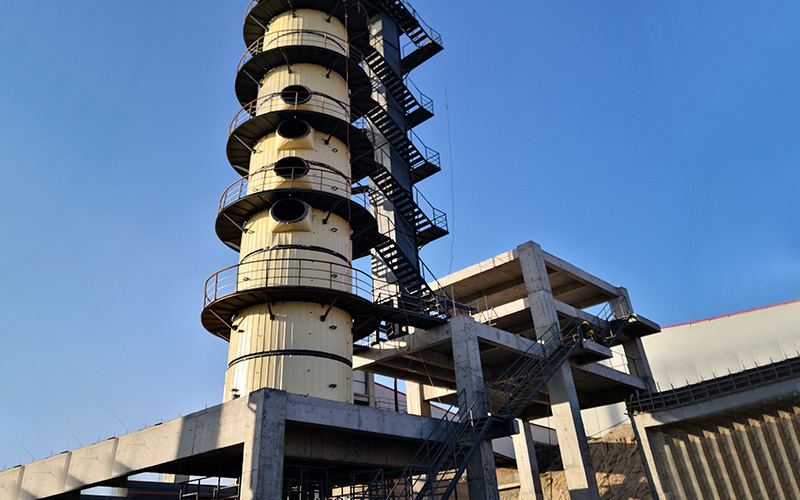
Carbon material drying production line
Production Line Introduction:The new vertical drying production line adopts our company's patented technology for a unique internal structure design, achieving full contact between the material and hot flue gas during the drying process, conducting multiple heat exchanges in a deflection manner, resulting in uniform heating of the material and high thermal efficiency; carbon materials fall in a creeping manner through the annular space between the inner and outer cylinders, with the materials almost in a stationary state, effectively reducing the wear and damage rate between the materials.
The new vertical drying production line is different from horizontal rolling dryers, as it adopts static drying. The entire equipment remains stationary, and the production process includes material conveying system, dry foam conveying system, main drying system, discharge system, finished product conveying system, dust removal system (for carbon materials, finished products, and main body dust removal), hot air system, compressed air, nitrogen, power supply system, and control system. The kiln body is the core part of the entire system, and during production, the kiln body serves as the core to achieve fully automatic control of the entire production system.
Production Capacity:20 tons to 50 tons/hour
Heat Source:Hot air furnace flue gas, high-temperature flue gas from the kiln tail.
Prominent Advantages
(1) The new vertical drying production line has low energy consumption per unit of dried material, with extremely significant energy-saving effects.
(2) The overall damage rate during the drying process is low.
(3) The moisture quality control of the dried lignite is stable.
(4) The equipment occupies a small area.
(5) Low operating costs of the equipment: Due to the new vertical drying production line adopting a static equipment approach for nearly static drying, the stability of the equipment is greatly improved, and the material in the dryer slowly creeps down, resulting in minimal equipment wear.
Process Flow
(1) Material Conveying System
Wet carbon is delivered from the coking area to the top of the wet carbon buffer bin in this system via the raw material belt. Additionally, there is a fuel coke foam conveying system that sends dry coke foam to the fuel storage bin of the carbon drying system for use in the hot air furnace. The raw material belt conveyor automatically replenishes the material based on the height of the material level at the top of the wet carbon buffer bin. The wet carbon buffer bin can accommodate the required storage of wet carbon for the process, allowing for automatic continuous production in the drying furnace. The wet carbon buffer bin automatically replenishes the drying furnace through a vertical large-angle belt based on the material level height in the drying furnace, and the wet carbon bin shares a frame with the bubbling furnace. To avoid the use of the tail sweeper or emergency discharge at the top of the wet carbon buffer bin, a vertical pipeline is installed at the tail of the machine, with the end of the pipeline connected to the coke foam fuel bin.
(2) Dry Coke Powder Conveying System
Dry coke foam is pneumatically conveyed from the screening and distribution station to the fuel bin in the carbon drying area (with a volume that meets the daily fuel requirement when the drying kiln uses coke foam). The size and installation height of the fuel bin are reasonably designed, and the top of the fuel bin is connected to a vertical discharge pipe coming down from the top of the wet carbon bin. The lower part of the fuel bin uses a material conveying device (preferably a scraper conveyor + disc feeder) to send the coke foam into the hot air furnace.
(3) Main System
The main system primarily receives wet carbon delivered by the raw material conveying system via a vertical large-angle belt conveyor, and sends the wet carbon into the dryer through a receiving plate and distributor. The vertical dryer consists of an outer, middle, and inner cylindrical body and a guide plate. The space between the outer and middle cylindrical bodies forms a waste gas channel with 8 partitions, while the middle and inner cylindrical bodies form an annular material channel. Under the influence of gravity, the material creeps into the material layer and gradually dries. The outer and inner circles of the material layer ensure that the material is evenly distributed in the annular material layer and is divided into 8 compartments by the material layer partitions, achieving precise control of the dryer. The outer and inner circles of the material layer maximize the passage of hot air while blocking the entry and exit of materials.
(4) Hot Air System
The main heat source pipeline of the carbon dryer connects to the hot air furnace, with a bypass connecting to other available high-temperature flue gas. When the air volume and temperature cannot meet the dryer’s requirements, hot air is supplemented by the hot air furnace. Air is sent into the hot air furnace by a blower, where low-temperature hot air is generated by burning carbon material coke foam. The hot air then passes through the secondary furnace chamber, divided into multiple air ducts entering the drying furnace from different heights. Under the influence of the airflow guide plate and negative pressure principle, the hot air fully exchanges heat with the wet carbon in the material layer, removing excess moisture before entering the tail process dust collector through multiple pipelines. After purification and dust removal, the hot air is discharged to meet standards. The air duct after the hot air furnace is equipped with an automatic control valve to facilitate adjustment of the air volume based on temperature.
(5) Discharge System
The discharge bin of the dryer is equipped with motorized vibrating feeders corresponding to 8 discharge outlets, which unload the finished product into the finished product buffer bin through the vibrating feeders. The bottom of the buffer bin is equipped with an electric hydraulic flap valve, a double-layer heavy hammer lock valve, and a (pneumatic) distribution three-way valve, which unloads the carbon onto the finished product belt, sending it to the transfer station. To facilitate initial startup or timely discharge in case of red material in the furnace, an emergency belt conveyor is set up on the other side of the three-way valve for emergency discharge.
(6) Dust Removal System
The waste gas dust removal system adopts a negative pressure type, with a low-pressure pulse bag dust collector. The collected dust is lifted to the dust collection ash bin. For the vertical drying equipment, due to the use of low-temperature drying principles and the repeated passage of hot air through the material, the initial temperature of the hot air entering the two dust removal devices is around 70°C. The energy-saving effect is significant in spring, summer, and autumn, but condensation is likely in winter. Therefore, in addition to ensuring the insulation of the dust collector, a DN250 hot air pipe is bypassed from the air inlet of the dryer to the air outlet of the dryer, with an electromagnetic butterfly valve installed in between to control its opening degree. This ensures that in winter, the temperature of the hot air entering the dust collector is around 90°C, increasing the temperature of the hot air entering the dust collector to avoid condensation. When spring arrives and temperatures rise, the electromagnetic butterfly valve is closed, allowing all hot air to directly enter the dryer, improving hot air efficiency. Finally, the flue gas is purified and treated by the dust collector before being discharged into the atmosphere through the fan and chimney, with a dust concentration of ≤10mg/Nm3.
Process Flow Diagram
Technical Parameters
Capacity (t/h)
|
20 ⁓ 50
|
Processed Material
|
Lanthanoid carbon, coke, carbide slag, coal slurry, lithium battery silicon material
|
Material Particle Size / mm
|
5 ⁓ 35
|
Initial Moisture Content of Material / %
|
≤20
|
Moisture Content of Dry Product / %
|
≤1
|
Crushing Rate / %
|
≤2
|
Product Temperature / ℃
|
≤120
|
Flue Gas Temperature / ℃
|
≤85℃ (before entering the bag filter)
|
Standard Coal Consumption (Kg/ton)
|
≤32
|
Dry Basis Lanthanoid Carbon Power Consumption (KWh/ton)
|
≤15
|
Flue Gas Emission Concentration (mg/Nm3)
|
≤10
|
Number of Working Days per Year / days
|
≥330
|
Number of Operators / (people / shift)
|
2⁓3
|
Get more solutions for free
If you are interested in our products, please leave your email, we will contact you as soon as possible, thank you!