Expert of Systematic Overall Solution for Calcium Material Resource Utilization
-
ProductPioneer In Calcium Material Industry Services, Renowned Globally For Exceptional Quality.Marketing & ServiceNational Service Hotline:
-
SolutionEngineering Service Provider Empowering New Technologies For Calcium Carbonate.Marketing & ServiceNational Service Hotline:
-
CaseExperts In Calcium Stone Industry Engineering With A Deeper Understanding Of Craftsmanship.Marketing & ServiceNational Service Hotline:
-
InnovationSurvive By Quality, Develop Through Innovation.Marketing & ServiceNational Service Hotline:
-
BlogsPeople-Oriented, Advocating Technology, Customer First, Win-Win Cooperation.Marketing & ServiceNational Service Hotline:
-
AboutInnovator In Calcium Materials Industry, Global Service Leader.Marketing & ServiceNational Service Hotline:
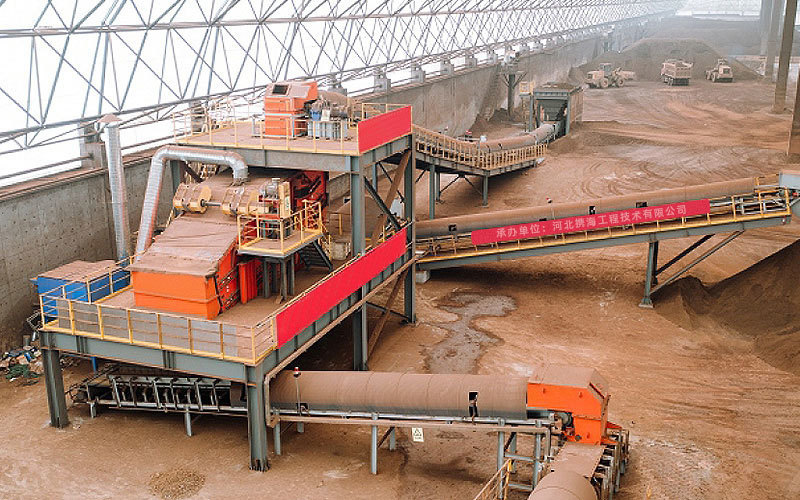
Block Ore Screening Production Line
Introduction to the block ore screening production line:The production line is centered around large tension screens, banana screens, or linear screens, equipped with auxiliary facilities such as hoppers, drag belt scales, belt conveyors, bucket elevators, and environmental dust collectors. It is reasonably planned and arranged according to the actual site conditions of the customer, ultimately forming an intelligent and environmentally friendly material screening and processing system. The production line selects vibrating screens based on material characteristics to achieve material dispersion and screening, addressing the issue of material agglomeration, and providing good screening results for sticky and wet materials. This production line is not only used for processing block ore in ironmaking plants in the metallurgical industry but is also widely applied in industrial fields such as coal, sand and gravel aggregates, potassium salt, mining, grain, and oil shale.
Capacity:50 tons 5000 tons/hour (depending on grading particle size)
Highlight Advantages
(1) The system generates low noise, has a long lifespan for the vibrating screen, and the screen plates are easy to replace.
(2) It can be used for both dry and wet screening, significantly reducing the limit rate of the screened material, allowing for the selection of small pieces, thus generating benefits.
(3) It can be configured in various combinations of single-layer, double-layer, or triple-layer screens.
(4) The screen plates have a large processing capacity per unit area and high screening efficiency, widely used for screening operations of difficult materials such as medium and fine particles, high viscosity, and wet materials.
(5) The system has low dust pollution, minimal dust generation, clean and environmentally friendly workstations, and meets environmental protection requirements.
Process Flow
Material Conveying: Mainly consists of receiving hoppers, drag belt scales, belt conveyors or bucket elevators, weighing devices, electromagnetic iron removers, etc. The material to be screened is delivered to the receiving hopper by a loader, and the quantified material is conveyed to the vibrating screen feed inlet via the drag belt scale, belt conveyor, or bucket elevator.
Material Screening: The main body consists of various types of vibrating screens, such as linear screens, banana screens, tension screens, drum screens, etc. The material in this unit is separated by various levels of screen plates and then falls onto the belt conveyor after screening, and is then conveyed to the corresponding particle size storage area or silo.
When the production line is put into operation, the material is first pushed to the receiving hopper to ensure that the hopper is not empty. The system can achieve one-click start control, sequentially opening the post-screening belt conveyor, vibrating screen, pre-screening belt conveyor (bucket elevator), and drag belt scale, allowing the material to enter the screening processing system. When stopping the production line, the order of equipment shutdown is the opposite of the startup, and the interval time for starting and stopping each device can be set according to the material characteristics and on-site debugging conditions. The hourly processing capacity can be specified on the control screen. Each device is equipped with a fault alarm function to promptly inform the main control personnel about the equipment operation status.
The production line is equipped with a dust removal system, with dust removal points mainly set at the discharge points, such as the discharge point of the drag belt scale, the discharge point of the belt conveyor head, and the vibrating screen has an independent dust collection port. The dust removal air volume can maintain a negative pressure state at each dust generation point to prevent dust leakage, and the discharge indicators after filtration by the dust collector meet environmental protection requirements.
Technical Parameters
Capacity (t/h) | 50 ⁓ 5000 |
Main Equipment | Main Supporting Equipment Models and Technical Economic Indicators |
Screen Width (mm) | 1000 ⁓ 5200 |
Screen Length (m) | 4 ⁓ 12 |
Inclination Angle (°) | 5 ⁓ 30 |
Particle Size Processing Range (mm) | 3 ⁓ 80 |
Qualified Rate of Screened Material (%) | >92 |
Screening Efficiency (%) | 80 ⁓ 90 |
Screen Mesh Life (h) | 4000 ⁓ 6000 |
Vibrator Service Life (years) | >10 |
Processed Materials | Block Ore, Raw Coal, Potash Salt, Grain, Sand and Gravel Aggregate |
Get more solutions for free
If you are interested in our products, please leave your email, we will contact you as soon as possible, thank you!
COOKIES
Our website uses cookies and similar technologies to personalize the advertising shown to you and to help you get the best experience on our website. For more information, see our Privacy & Cookie Policy
COOKIES
Our website uses cookies and similar technologies to personalize the advertising shown to you and to help you get the best experience on our website. For more information, see our Privacy & Cookie Policy
These cookies are necessary for basic functions such as payment. Standard cookies cannot be turned off and do not store any of your information.
These cookies collect information, such as how many people are using our site or which pages are popular, to help us improve the customer experience. Turning these cookies off will mean we can't collect information to improve your experience.
These cookies enable the website to provide enhanced functionality and personalization. They may be set by us or by third-party providers whose services we have added to our pages. If you do not allow these cookies, some or all of these services may not function properly.
These cookies help us understand what you are interested in so that we can show you relevant advertising on other websites. Turning these cookies off will mean we are unable to show you any personalized advertising.
Telephone
Company Address
Weier Business 801, No. 92 Huai'an East Road, Yuhua District, Shijiazhuang City, Hebei Province