Expert of Systematic Overall Solution for Calcium Material Resource Utilization
-
ProductPioneer In Calcium Material Industry Services, Renowned Globally For Exceptional Quality.Marketing & ServiceNational Service Hotline:
-
SolutionEngineering Service Provider Empowering New Technologies For Calcium Carbonate.Marketing & ServiceNational Service Hotline:
-
CaseExperts In Calcium Stone Industry Engineering With A Deeper Understanding Of Craftsmanship.Marketing & ServiceNational Service Hotline:
-
InnovationSurvive By Quality, Develop Through Innovation.Marketing & ServiceNational Service Hotline:
-
BlogsPeople-Oriented, Advocating Technology, Customer First, Win-Win Cooperation.Marketing & ServiceNational Service Hotline:
-
AboutInnovator In Calcium Materials Industry, Global Service Leader.Marketing & ServiceNational Service Hotline:
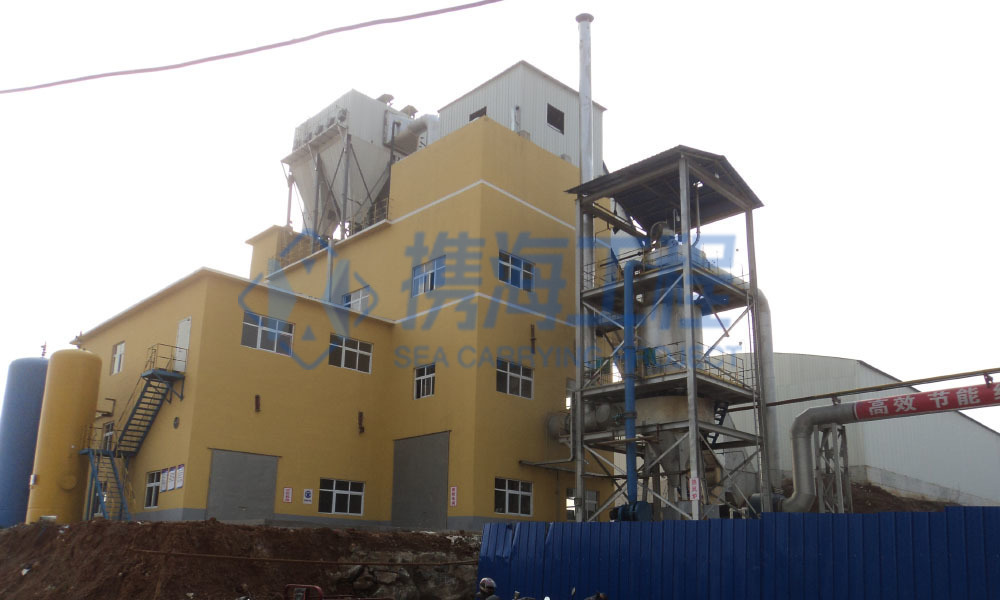
Powder production line
Introduction to the grinding powder production line:The new grinding powder production line coal powder preparation station project consists of raw coal storage and transportation system, grinding system, powder collection system, flue gas furnace system, and electrical and instrumentation automation system. It is widely used in industries such as cement, electricity, steel, and metallurgy. The grinding system can use vertical coal mills or horizontal ball mills, and the powder selection equipment uses variable frequency motor speed control, allowing for control of the powder fineness by adjusting the inverter. The flue gas furnace system provides hot flue gas to the coal mill, serving as the medium for coal powder drying and blowing. The grinding powder production line integrates conveying, grinding, drying, and powder selection into one, with a fully enclosed design that greatly reduces dust emissions.
Production capacity:3 tons 30 tons/hour
Heat source:Hot air furnace flue gas.
Prominent Advantages
(1) Higher selection rate, improving economic benefits.
(2) Large system capacity, high system safety.
(3) Compact system design, smooth material transportation.
(4) Low dust pollution, minimal dust, clean and environmentally friendly workstations, meeting environmental protection requirements.
(5) Reasonable project cost, high input-output ratio.
Process Flow
(1) Raw Coal Storage and Supply System
The raw coal storage system is designed as a dry coal shed, and the coal supply facilities consist of a set of coal feeding equipment and a coal loading system. Its task is to accept qualified washed coal transported by trucks and deliver it to the raw coal bin in the main workshop of the pulverizing preparation room. Qualified raw coal is transported into the dry coal shed by trucks and is piled, stacked, and supplied using a loader and other auxiliary machinery. During coal supply, the loader transports the coal into the receiving hopper, from where it is sent to the raw coal bin in the pulverizing room by a coal feeder and a high-angle belt conveyor (bucket elevator).
(2) Pulverizing System
The pulverizing system includes: raw coal bin, coal feeder, coal mill, bag dust collector, coal powder bin, coal powder fan, and related process pipelines.
Raw coal is sent from the coal supply system to the raw coal bin, enters the pulverizing system, and is fed into the coal mill through various gates and the coal feeder. In the mill, drying and grinding of the coal occur simultaneously. After grinding, the coal powder undergoes mass and heat transfer with hot air at 200℃ to 350℃, with moisture transferring from the coal powder into the flue gas, and the coal powder being dried by the hot air. Subsequently, the coal powder enters the classifier with the airflow, where the selected coarse powder returns to the mill for further grinding, while the fine powder continues to be drawn in by the coal powder fan, entering the bag dust collector, where it is separated and falls into the coal powder bin.
After filtering through the bag dust collector, the gas meets national emission standards and is discharged into the atmosphere. The entire pulverizing system operates under negative pressure. During the grinding process in the coal mill, larger hard materials in the coal, such as stones and coal gangue, are expelled to the slag box by the rotating scraper for regular cleaning.
(3) Flue Gas Furnace System
The medium used for drying is mainly a mixture of flue gas produced by the flue gas furnace and air, with a drying gas temperature generally ranging from 200 to 350℃. A flue gas furnace system requires one flue gas furnace, which is equipped with a set of burners, with a combustion capacity of 2500 Nm3/h, using self-produced coal powder as fuel, and the ignition method for the flue gas furnace is automatic ignition. There are flue gas pipelines and equipment such as shut-off valves and regulating valves between the flue gas furnace and the mill.
The flue gas furnace system is arranged outside the workshop for pulverizing and conveying coal, in an open-air layout, with the furnace body sitting on a raised platform, and other pipelines and valves arranged overhead. A maintenance platform is provided at the valve location. The system control for the flue gas is uniformly arranged in the operation room of the pulverizing and conveying workshop.
Process Flow Diagram
Technical Parameters
Production Capacity (t/h) | 5⁓6 | 7⁓8 | 10⁓12 | 15⁓18 | 20⁓24 |
Main Equipment | Main Supporting Equipment Models and Technical Economic Indicators | ||||
Mill Diameter/mm | 1100 | 1200 | 1300 | 1500 | 1700 |
Mill Power/kw | 132+11 | 180+18 | 200+22 | 280+30 | 315+37 |
Coal Powder Separator | FGM64-7(M) | FGM96-2×4(M) | FGM96-2×5(M) | FGM96-2×7(M) | FGM96-2×10(M) |
Hot Air Furnace Air Volume/Nm3 | 15000⁓18000 | 22000⁓25000 | 31000⁓34000 | 46000⁓55000 | 62000⁓75000 |
Coal Powder Fineness⁓200 Mesh/% | ≥90 | ||||
Coal Powder Moisture/% | ≤2 | ||||
Hot Air Inlet Temperature/℃ | 220 ⁓ 350 | ||||
Mill Outlet Temperature/℃ | 60 ⁓ 70 | ||||
Flue Gas Emission Concentration (mg/Nm3) | ≤30 | ||||
Annual Working Days/Days | ≥330 | ||||
Number of Operators/(people/shift) | 2⁓3 |
Get more solutions for free
If you are interested in our products, please leave your email, we will contact you as soon as possible, thank you!
COOKIES
Our website uses cookies and similar technologies to personalize the advertising shown to you and to help you get the best experience on our website. For more information, see our Privacy & Cookie Policy
COOKIES
Our website uses cookies and similar technologies to personalize the advertising shown to you and to help you get the best experience on our website. For more information, see our Privacy & Cookie Policy
These cookies are necessary for basic functions such as payment. Standard cookies cannot be turned off and do not store any of your information.
These cookies collect information, such as how many people are using our site or which pages are popular, to help us improve the customer experience. Turning these cookies off will mean we can't collect information to improve your experience.
These cookies enable the website to provide enhanced functionality and personalization. They may be set by us or by third-party providers whose services we have added to our pages. If you do not allow these cookies, some or all of these services may not function properly.
These cookies help us understand what you are interested in so that we can show you relevant advertising on other websites. Turning these cookies off will mean we are unable to show you any personalized advertising.
Telephone
Company Address
Weier Business 801, No. 92 Huai'an East Road, Yuhua District, Shijiazhuang City, Hebei Province