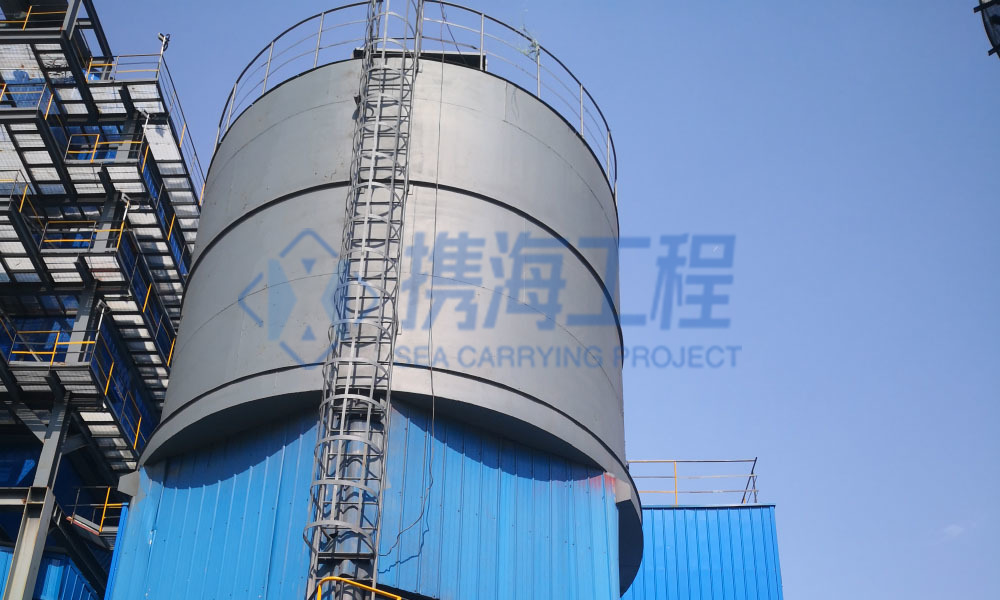
Humidification and Mixing Production Line
Introduction to the humidifying mixing production line:The humidifying mixing production line is a device used for humidifying and mixing industrial powder materials. Its working principle mainly includes three aspects: humidification, mixing, and control. The main equipment of the production line is the mixer, which has several water inlets on its shell connected to the water supply pipeline. The nozzle of the mixing device sprays water into a mist and releases it onto the surface of the powder being mixed, increasing the humidity in the mixing chamber. The rapid rotation of the mixing device or blades inside the mixer stirs and mixes the powdered materials. The mixed wet material contains a certain amount of moisture and can be unloaded onto the transportation machinery of trucks through conveying machinery, with no dust during the unloading process. Through the control panel, users can set parameters such as mixing time, speed, and humidity level. The control panel converts the settings into electrical signals to control the operation of the machine and the humidification function. The humidifying mixing production line is efficient and environmentally friendly, widely used in industries such as chemical metallurgy, electric power, mining, environmental protection, and building materials.
Production capacity:10 tons 200 tons/hour
Outstanding Advantages
(1) Two sets of spiral blades are used for stirring, which has high stirring efficiency and occupies less space.
(2) The stirring blades of the mixer are made of high wear-resistant special alloys or ceramics, ensuring a long service life.
(3) The equipment operates smoothly with low noise.
(4) The equipment is easy to maintain and has the advantages of high efficiency and time-saving.
(5) The system has low dust pollution and minimal dust generation, keeping the work environment clean and environmentally friendly, in compliance with environmental protection requirements.
Process Flow
(1) Dry Powder Material Conveying System
The system mainly consists of: conveying pipeline, single machine bag dust collector, dry powder silo, etc. The tanker transports dry powder material to the dry powder silo through pneumatic conveying via the conveying pipeline. A single machine bag dust collector is installed at the top of the silo, and the compressed air used for conveying the powder is filtered before being discharged into the atmosphere, meeting environmental protection requirements.
(2) Humidification and Mixing System
The system mainly consists of: star-shaped unloading valve, screw conveyor, humidification mixer, etc. In this stage, dry powder material is mixed and stirred with water to produce wet material.
When the system starts, the operator clicks the "one-click start" button on the control box. First, the humidification mixer automatically starts, then the lower screw conveyor automatically starts, followed by the upper screw conveyor, and finally the star-shaped unloading valve automatically starts. The star-shaped unloading valve has a delayed start time (set according to on-site debugging time) for the water supply system's solenoid valve to automatically open. Before the star-shaped unloading valve starts, the unloading sulfurization system at the bottom of the silo automatically opens. Dry powder material is unloaded from the powder silo to the humidification mixer for humidification processing.
When the material silo sends a low material level signal, the unloading valve at the bottom of the silo automatically stops, and the system automatically executes the "one-click stop" program, while the system issues a low material level alarm signal.
When the system needs to stop working, the operator clicks the "one-click stop" button on the control box. First, the star-shaped unloading valve automatically stops; after a set delay time, the upper screw conveyor automatically stops; after another set delay time, the lower screw conveyor automatically stops; after a delay, the solenoid valve of the water supply system automatically closes. Finally, the humidification mixer automatically stops.
Each device's start and stop are set to manual/automatic switching mode. The conveying capacity of each device is adjusted through frequency input, with the lower screw conveyor having a weighing function, displaying the hourly dry material conveying capacity on the control interface. The system pressure, flow rate, and equipment operating status are all displayed on the operation interface.
(3) Water Supply System
The system mainly consists of: water tank, water pump, electric regulating valve, electromagnetic flow meter, solenoid valve, water supply pipeline, etc.
By inputting the opening of the electric regulating valve, the water supply amount is adjusted, and the results are displayed on the control interface through the electromagnetic flow meter. The system provides constant pressure water supply. When the opening of the regulating valve changes, the system pressure is adjusted with the water pump using PID control, maintaining the system pressure at a set value of 0.3-0.8Mpa, and a constant pressure and quantitative water source is sent to the evenly distributed spray ports of the humidification mixer for mixing operations.
The lower limit of the water tank is interlocked with the submersible pump, solenoid valve, and water pump in the water supply pipeline. When the water tank sends a low water level signal, the solenoid valve opens, and the submersible pump starts; when the water tank sends a high water level signal, the submersible pump stops, and the solenoid valve closes; when the water tank sends an ultra-low water level signal, the water pump stops working, and the system automatically executes the "one-click shutdown program."
The start and stop of the water pump are set to manual/automatic switching mode. The water pump flow rate is adjusted through frequency input. The system pressure, flow rate, and equipment operating status are all displayed on the operation interface.
(4) Compressed Air Sulfurization System
The dry powder silo is equipped with a sulfurization device at the bottom, controlled by a solenoid valve for the gas source, with sulfurization controlled by time intervals. The system pressure, flow rate, and equipment operating status are all displayed on the operation interface.
Technical Parameters
Capacity (t/h) | 10 | 20 | 40 | 60 | 80 | 100 | 200 |
Main Equipment | Main Supporting Equipment Models and Technical Economic Indicators | ||||||
Screw Diameter (mm) | Ø400 | Ø400 | Ø600 | Ø600 | Ø700 | Ø700 | Ø800 |
Mixer Power (kw) | 4.0 | 5.5 | 11 | 15 | 18.5 | 22 | 30 |
Inlet Flange | DN50 | DN50 | DN100 | DN100 | DN100 | DN100 | DN100 |
Water Pressure (MPa) | 0.4 ⁓ 0.8 | ||||||
Moisture Content (%) | 15 ⁓ 20 |
Get more solutions for free
If you are interested in our products, please leave your email, we will contact you as soon as possible, thank you!