Expert of Systematic Overall Solution for Calcium Material Resource Utilization
-
ProductPioneer In Calcium Material Industry Services, Renowned Globally For Exceptional Quality.Marketing & ServiceNational Service Hotline:
-
SolutionEngineering Service Provider Empowering New Technologies For Calcium Carbonate.Marketing & ServiceNational Service Hotline:
-
CaseExperts In Calcium Stone Industry Engineering With A Deeper Understanding Of Craftsmanship.Marketing & ServiceNational Service Hotline:
-
InnovationSurvive By Quality, Develop Through Innovation.Marketing & ServiceNational Service Hotline:
-
BlogsPeople-Oriented, Advocating Technology, Customer First, Win-Win Cooperation.Marketing & ServiceNational Service Hotline:
-
AboutInnovator In Calcium Materials Industry, Global Service Leader.Marketing & ServiceNational Service Hotline:
The structure of the desulfurization spray tower.
Dec 16,2024
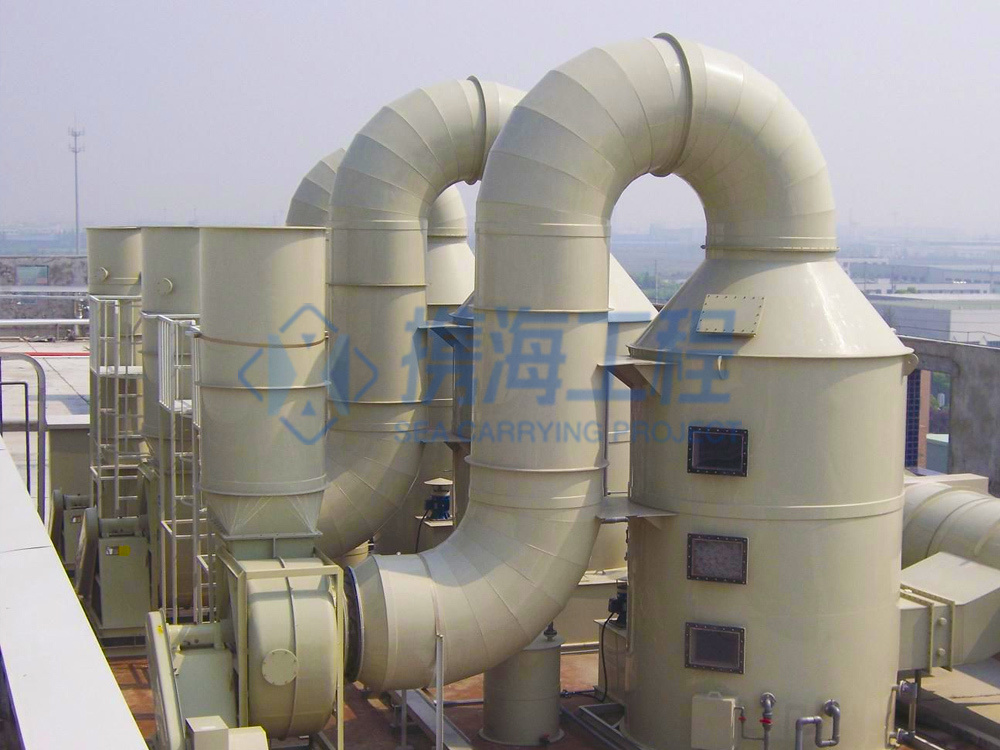
Wet flue gas desulfurization technology (FGD) is widely used in large and medium-sized thermal power plants due to its high desulfurization rate, wide applicability of coal quality, mature process technology, long stable operation cycle, small impact of load changes, and large flue gas treatment capacity. It has become the dominant process technology for flue gas desulfurization in thermal power plants both domestically and internationally. However, due to the strong corrosiveness of the medium, high flue gas temperature, high solid content of SO2 absorption liquid, and significant scouring effect, the construction technology quality requirements are relatively high. Therefore, corrosion control of the desulfurization spray tower has always been one of the key issues affecting the long-term safe operation of the equipment.
Our company's selection of anti-corrosion structures for desulfurization comprehensively considers the following aspects:
(1) Meeting anti-corrosion requirements under complex chemical conditions: The chemical environment is complex, with high acid content in the flue gas, and the condensate formed on the inner lining surface has strong corrosiveness to most construction materials, so the lining material is required to have strong acid corrosion resistance;
(2) Temperature resistance requirements: The temperature of the flue gas varies greatly, with the wet flue gas desulfurization temperature between 150°C and 200°C, requiring the lining to have the ability to withstand temperature changes, ensuring it does not crack and is durable;
(3) Good wear resistance: The flue gas contains a large amount of dust, and under the action of corrosive media, the actual wear may be quite significant, so the anti-corrosion material is required to have good wear resistance;
(4) Good adhesion: The anti-corrosion material must have strong adhesion strength, which not only refers to the high adhesion strength of the material itself but also to the high adhesion strength between the material and the substrate. Additionally, the material should not easily crack, delaminate, or peel off, with good adhesion and impact strength, thus ensuring good corrosion resistance. Typically, we require the adhesion strength of the primer material to the steel structure foundation to reach at least 10 MPa.
Previous article
COOKIES
Our website uses cookies and similar technologies to personalize the advertising shown to you and to help you get the best experience on our website. For more information, see our Privacy & Cookie Policy
COOKIES
Our website uses cookies and similar technologies to personalize the advertising shown to you and to help you get the best experience on our website. For more information, see our Privacy & Cookie Policy
These cookies are necessary for basic functions such as payment. Standard cookies cannot be turned off and do not store any of your information.
These cookies collect information, such as how many people are using our site or which pages are popular, to help us improve the customer experience. Turning these cookies off will mean we can't collect information to improve your experience.
These cookies enable the website to provide enhanced functionality and personalization. They may be set by us or by third-party providers whose services we have added to our pages. If you do not allow these cookies, some or all of these services may not function properly.
These cookies help us understand what you are interested in so that we can show you relevant advertising on other websites. Turning these cookies off will mean we are unable to show you any personalized advertising.
Telephone
Company Address
Weier Business 801, No. 92 Huai'an East Road, Yuhua District, Shijiazhuang City, Hebei Province